A functional test is a quickest and most effective way to check an assembly function as designed. This simulates the intended field of application and also analyses the electrical behaviour of the assembled board. Read more to find out our top 7 checks and how we fixed defects during a recent project.
Firstly, the assembly process is chosen depending on the customer’s requirements and the electronic components. A mixed process of through-hole and SMT assemblies was used to build these boards. Next, once the PCBA is ready, it undergoes functional testing or FCT before being shipped. These tests aim to eliminate any defects or faults that might hinder reliability, replace incorrect or faulty components, check solder points and generate a detailed report to share with our customers.
This module will be used in an EV charging station. Certain specific components were provided by the customer and others were sourced from our suppliers.
The 7 Checkpoints We Ran To Ensure The Proper Functioning Of A PCBA:
At Ark Circuitry, we go the extra mile to ensure reliable boards are manufactured. For this specific project, after uploading the code, the engineer tests the boards to ensure the board will carry out the intended functions in the actual application. The checkpoints that they look at ticking off are:
1. Relay check:
According to the functions and design, we have used 5 relays on the board. When the engineer inputs the command, a soft clicking noise is the expected output.
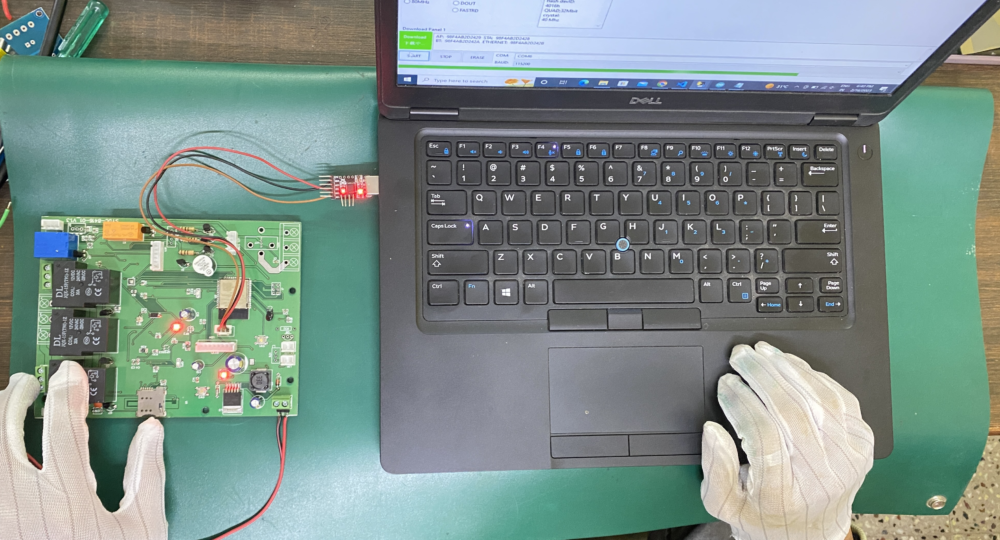
2. Buzzer test:
The next is the buzzer test. The buzzer must go off when the command is run to confirm its functioning.
3. GSM module and Wifi test:
A Sim card is inserted and the code is run. This test records the HSN code of the network and IP addresses generated.
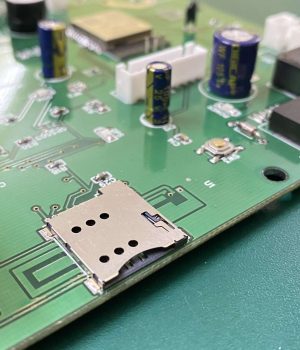
4. CAN test:
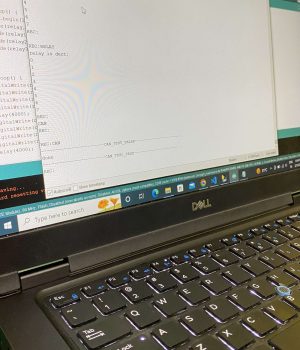
The Controller Area Network or the CAN test. When the command is given, the output returns as a pass and that signifies its functioning.
5. RFID test
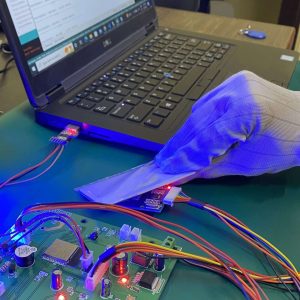
6. LED check
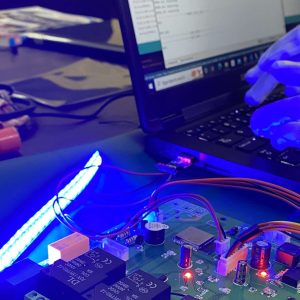
7. Voltage check:
An input power of 12V is fed and an output of 5V is recorded to ensure its functioning. If a defect is detected, they check for open/shorts in nets or faults in solder connections.
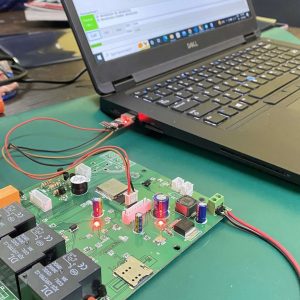
Lastly, once the tests are complete, the data is processed and the results generated. The stored data would aid in maintaining the PCBA quality effectively. A detailed report on the status of functioning is shared with the customer for analysis or to refer to the test log.
Some points to look for when a fault persists:
- Check and recheck that all IC pins are soldered properly
- Ensure that there is no solder paste residue
- Reflow oven: When the outer layer of the solder paste would have dried and the inner layer might be still wet it leads to no contact. Check if it has been soldered well.
- Do not use solder paste that might be old or not stored at the right temperature. Temperature and environment are crucial, this results in no solder
- Manual solder any joints where there is no contact
- Use reliable and good-quality components
- Ensure your engineers are well-trained from time to time and quick to pick up issues/faults